Solvay and Aerosint collaborate on 3D printing specialty polymers
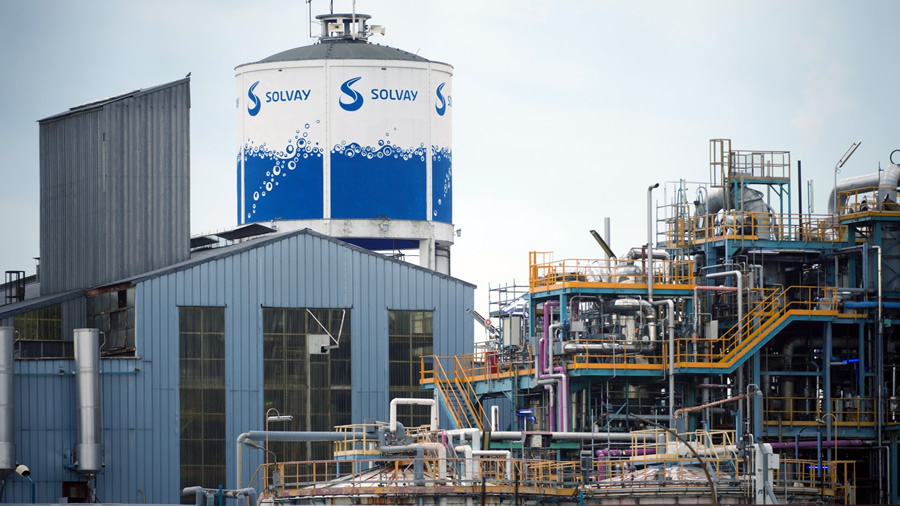
Solvay has entered a research collaboration agreement with Aerosint to develop an economically viable SLS printing process for high-performance polymers. High-performance polymers such as Ketaspire polyetheretherketone (PEEK) and Ryton polyphenylene sulphide (PPS) have the potential to open new avenues for additive manufacturing (AM) in demanding applications, but their adoption with key powder fusion technologies such as selective laser sintering (SLS) remains limited today.
“SLS machines that can process high temperature polymers are carefully designed and assembled with sophisticated and expensive components. However, at present, there is a significant operating cost disadvantage during the build, which is the excessive waste of up to 90 percent of ‘used-but-unfused’ powder,” said Edouard Moens, managing director, Aerosint. “Our patented spatially-selective, multiple-powder deposition system under development incorporates a non-fusible support material in each layer where expensive high-performance polymers are not required, thereby reducing material waste to very low levels.”
Solvay has been cooperating with Aerosint for over two years, supporting the development of their game-changing technology with advanced material, process and fusion expertise. “As with all innovative, ground-breaking technologies, there are many challenges to overcome. One of them is to develop and fully optimize high-performance AM polymer powders for use at high temperatures alongside non-fusible materials in a multi-powder deposition process,” says Brian Alexander, global product and application manager for additive manufacturing at Solvay’s Specialty Polymers global business unit.
“Not only will this technology make 3D printing of high-performance polymers more affordable, it also will open up its enormous potential to become a competitive industrial process for AM system manufacturers in the medical, aerospace and automotive sectors.
Source: Rubber World Magazine